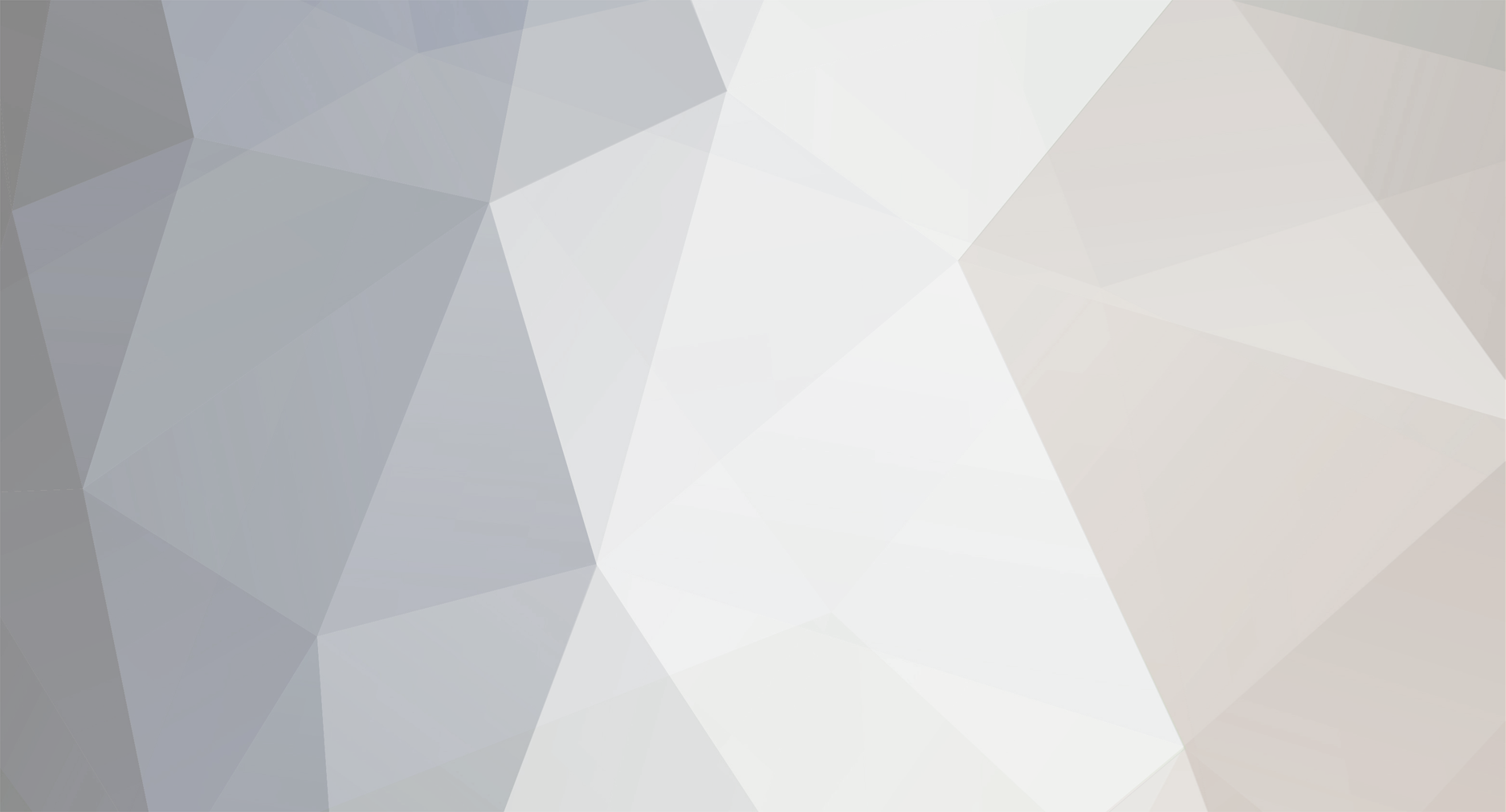
verne
Members-
Posts
74 -
Joined
-
Last visited
-
Days Won
2
verne last won the day on December 20 2009
verne had the most liked content!
About verne
- Birthday 06/02/1953
Profile Information
-
Occupation
Motor mechanic
verne's Achievements
Newbie (1/14)
1
Reputation
-
mould will always grow where there is food and moisture for it. a lot of it is bad for the health too. i think part of your problem is likely to be your painted walls. modern plastic emulsion paints aren't breathable - in fact they are so good they can be used as an isolator coat between paints of different (incompatible) types to prevent reactions between them... using these for decoration instead of the more traditional whitewashes or limewashes (or nothing at all) will seal off the wall as if you have put a membrane over it, concentrating the escaping moisture into areas where the paint film has an insufficient bond or has otherwise broken down... i suggest you treat your mould with a dilute bleach solution and a scrubbing brush or a proprietory mould remover and forget about decorating until the damp is under control. anti-mould paints tend to be intended for use in areas of high levels of condensation, rather than areas that have a head of water pressure trying to push the paint from the walls. if the injection damp courses have worked well in the other houses, the chances of success with one in your house will be almost assured if it is of the same basic construction, certainly it will help and need not be tremendously expensive. the equipment can be hired to allow a diy job. if enough research is done first on methods, techniques and materials you will at least know that it wasn't a cowboy job... even when you have carried out all the damp reducing measures you can, it will take a long time for the moisture levels to stabilise and the real benefits of it can be seen - possibly a couple of years, or even longer! the vertical damp course is really worth a close look too. if the water table is naturally quite high in your area, rather than the ground being sodden just by drainage problems, you will definitely have to tackle the inside as well as having a close look at the footings if your house has any? a lot of houses do not have proper footings but were built simply on top of the ground, mostly on stone slabs that were set into the ground less than a foot... because lime and dung mortars were used, seasonal movements of the walls did not matter very much. a builder friend has just finished providing his own such house with a nice deep footing. he said it was "steady work" but not much of a problem.
-
i don't know much about stone built dwellings. a lot of the traditional peasant type houses were built of little more than rubble and were always damp and slightly better housing was built with cavity walls that had a decent stone facing but an infill of rubble and rubbish to keep the cost down... i suggest you investigate the possibility of a damp course of some sort before you begin spending much money on the place. an injection damp course probaly wouldn't be very successful alone - depending on the type of stone and construction the chemical would probably only saturate the mortar - but this type would be the cheapest option and would be bound to help. the electro-static damp course has fallen out of fashion and no one can tell me how they work but for most people most of the time they do work, or did work for those who had them. they are almost unknown now but rentokill installed thousands of them back in the 1960's. a deep vee of 3 or 4 inches is cut into the inside walls just above ground level and a continous copper strip is installed, the vee being filled with mortar to secure the strip. the two ends are passed through the wall and joined to a bronze fitting that i don't know the purpose of... fitting a membrane would be a huge amount of work, especially if the walls are thick and do have a rubble filled cavity. if it is possible to carry out some land drainage to reduce the amount of water in the ground around the house, this would probably make a great deal of difference in time, especially with the installation of a vertical damp proof course which will reduce the amount of wall accessible to the wet ground and further reduce the amount of damp. again the vertical dpc is little used now, but can be installed (relatively) quite easily in most instances by digging a short trench against the outside wall to expose the wall down to its footings. the wall is cleaned and rendered with a waterproof render and then covered with what was traditionally slate, but a waterproof membrane would probably be better and could possibly almost make the render redundant. working like this a short section at a time until the entire outside has been circumnavigated. the backfill of each section must be well compacted to ensure the walls remain stable. the same treatment can be given to the inside walls if damp remains a problem and the floors fitted with a membrane and insulation at the same time so your choice of floor coverings is not limited to breathable stuff. alternatively digging out and providing a (ventilated) cavity over which a loose laid concrete block floor is laid will also achieve the same object. please keep us posted.
-
it would be a good idea to try and minimise the damp if you can by attempting to trace the source and then taking a few precautions... an area that is naturally damp must be well ventilated and the source of the damp must not be covered with anything that can't breath... drylining the walls will probably drive more damp into the narrow strip between the floors dampening the woodwork... damp in solid walls can be caused by rising damp bridging the damp course (if it has one) in some way - perhaps by the internal plastering or because the ground level outside is too high or because a porous floor has been covered with something that is forcing an excess of moisture out to the walls. perhaps external rendering is too close to ground level. perhaps the ground is so saturated with water due to a faulty soakaway system or poor drainage. concrete paths too close to the house can cause excessive rain splash where rain bounces up from the hard surface a considerable distance and can saturate a wall above the damp course. damp in solid walls can also be caused by water ingress into the wall higher up and it not being able to escape into the ground because it has a damp course - gutters and downspouts, faulty or porous render can be the culprits. solid walls of old houses do often have damp in them naturally which would normally be kept to minimal levels by evaporation from the exposed brickwork outside. render is only suitable some of the time... if there is a high level of damp in your house you should be aware it does increase the risk of woodworm and dry rot attack. sensible timber treatment and good ventilation is the key to minimising the risk. the importance of open chimneys cannot be over-emphasised...
-
i have never seen one though i wouldn't be surprised if one existed. there are many light level switches available fitted to various devices from street lamps to night lights, including one that plugs in to a bulb holder. i suggest you approach one of the larger electrical wholesalers in your area - they often have access to consultants or at least tend to know their catalogues pretty well... if you get no success there i suggest you contact somebody like farnell or maplin or rs components who i am fairly sure will be able to supply something that could be installed within a switch.
-
the simple answer is - you can't! as far as i know there are no products that bond tiles to fresh air. i suggest you carry on removing the grout and any tiles not securely fixed until you have discovered the extent of the problem - then attempt to remove a few more tiles so you have an area of good solid plasterboard around the hole that it will be necessary to make by removing the sodden plasterboard. give it some drying time so your repair is not going to trap any moisture where it can cause long term damage. clean the edges of the resulting hole. don't worry if the hole isn't a regular shape - plasterboard repairs are more successful with irregular shapes as it provides more bonding area around the edge... if it is a stud wall with a cavity behind it you will need to provide a shoulder to prevent the patch from falling through the hole. you can do this by bonding some bits of board to the back of the existing plasterboard at convenient intervals around the hole leaving an inch or so protruding into the hole area... if it is a battened wall you can use the same method or provide extra battens or use a combination of the two methods. cut a patch to fit the hole from some board of the same thickness, but slightly smaller to leave a 3 or 4mm gap all around for the no-nails adhesive. glue (pva or similar) the patch into place against the shoulder and using spacers around the edge to maintain the gap until the glue is holding and then insert a bead of no-nails around the edge... if your plasterboard is just a dot and dab cladding over a solid wall it will be straightforward to provide a few dabs of adhesive and settle the patch until it provides a flush surface. the hard bit of the job will be removing the old tile adhesive without breaking any...
-
the victorians, like many from before and after, built many very good houses - but also threw up a lot of rubbish! a lot of the rubbish from the barratt type builders of those days is still standing - and i am living in one of them now. perhaps you are too? building materials were fairly expensive in those days, so was labour - in fact things weren't much different from now except there was no diesel lorries to haul stuff around and there was no power tools to make work quicker and easier. houses that were built for the letting market would have as many corners cut as were needed to bring them in within the budget... substandard mortar, bricks re-used from previous demolitions, substandard bricks, inner walls would be where any brick ends, cobbles and odd lumps of coal would be used up. the further up the house and at the back of the house was where most of the cost saving took place. a lot of money was saved by using second and third grade timber and adze cutting the rough sawn boards to fit - a lot of money was saved by having floorboards only planed one side... a lot of such houses were built without proper foundations or incorporating bits and pieces of the foundations of previous houses... half a ton would be a lot of weight to put on a floor upstairs if your house was without any defects. it would probably stand it quite safely until the floor began to become permanently warped as timber will if it is subjected to a great load for a long time. my concerns are about the unknown factors of the timber grades and the quality of the building and of the foundations. my advice is don't! if you must go ahead then pay a professional to look at it first so you can sue someone if there is a problem... if you have sufficient ceiling height in the room below you could strengthen the floor and spread the load into all the walls by installing more joists at right angles to the originals and underpinning your floor. you can then enjoy an open beam look or intall a new ceiling... alternatively a couple of nicely painted acro-props would provide extra support.
-
quickest and easiest thing to try first would be to use a different type of fire caulk. there must be many different types on the market with varying degrees of flexibility for different purposes. the problem is probably caused by the existing caulk being too rigid. i suggest you do some research into the local building and fire regulations where you are and find the purpose of that caulking; is it merely to stop smoke or is it to give a 30 minute fire barrier - or longer? armed with the correct requirements you can then approach some suppliers with your problem and requirements and obtain some really professional suggestions. one interesting solution which could allow a clearance for expansion is to use an intumescent sealer which would expand and seal the gap in the event of a fire... i believe there is also a variety of flexible and semi-flexible collars available for many types of pipe... even some of the high grade silicone sealers are resistant to some very high temperatures but remain very flexible - even in permanent contact with car exhaust systems... it probably was not necessary to use that method of sealing in the first place to overcome the problem. it was probably done that way to cut building costs. prepare for some resistance from the guys who have to fix it.
-
hello. traditional deep shine finishes take a lot of time and skill to achieve, although french polish takes considerably more skill than using coloured varnishes or stained wood and clear varnishes. i have produced some "nearly" french polish finishes with varnish by applying six or eight coats and flatting between coats using a fine wet or dry paper and a rubber block. the first couple of flattings were carried out dry with a 400 grade and thereafter wet with 600 grade. the last but one coat was flatted with 1200 grade with soap and water. the last coat had to be done in a very clean place with very clean materials and tools to eliminate the need to de-nib the final finish and the resultant polishing, although fine abrasive compound polishing will enhance the shine. modern mass produced stuff has more in common with car spraying than with traditional brush finishes. a cureable laquer is sprayed in huge volumes which buries minor surface defects and finds its own level while still semi-liquid but curing quickly in the same way araldite or body filler cures. the really hard finishes use some nasty chemicals in the curing process which means air fed breathing apparatus must be used, rather than just a face mask. i suggest you have a word or two with a painter at a local spray shop for suggestions. he will probably direct you to his paint supplier who should be able to mix a synthetic laquer to match your existing colour...
-
Replastering ceiling and spotlights...
verne replied to mgwdiynovice's topic in Plastering and Boarding
as long as you know exactly where your lights are going to be sited i think plaster first... if you are going to have to dig around a bit to avoid joists, it would be a good idea to to that before the plastering. might be a good idea to ask the plasterer what he thinks - plasterers aren't normal people and they tend to bite when upset... -
thanks for that info. i've not seen any clear stuff yet - pink and brown, and the stuff i generally use is the (almost the cheapest) white water based which does the job around the house ok. the stuff you speak of might be useful at work. sometimes things need to be stuck that would normally need a polyuerethane structural type adhesive which is expensive and has a very short life once the tube is started. i will buy a tube of clear and give it a try...
-
just a reminder to make certain the light/power is switched off first. when a bulb has failed it is easy to forget this little detail or become confused if there is more than one switch... water based no-nails will probably take longer than 15 minutes to set sufficiently due to the lack of absorbency of the materials to be stuck together. due to the difficulty of sticking glass to anything because of its smoothness its probably a good idea to scuff the surface a bit with some scotchbrite or fine wet-or-dry paper before you begin.
-
750mm is a wide span for a single louvred door. the construction of that type of door is not strong and to remove more than an absolute minimum of material for fitting is to invite problems for the future... i suspect the only way to fill the door hole with just one door would be to have one made especially for the purpose. who ever made it for you would probably have a good holiday this year on the proceeds... even using the double doors you have found would mean removing more than just a shaving or two from each door. in order to make them fit and have a couple of mm gap all around will mean removing 4 or 5 mm from the verticals and at least 40mm from the horizontals and could be more if your floor is carpeted... if the doors you have found are of particularly good quality you might get away with it, but i suggest you check with the supplier first. tell him your intentions and ask him if it will affect the warranty regarding warping and twisting... a more substantial solution would be to use a smaller size of louvred panel or panels, depending what is available and either have them fitted in place of the panels in a stock sized four or six panelled door or to have a substantial frame put around two smaller panels of a size to fill the space. it would still cost quite a bit though... it is not easy to give detailed instructions on door fitting in a post like this. there are quite a lot of how-to videos available. some are free off the internet. if you haven't a clue, then you probably don't have many tools either. might be a good idea to pay to have this one fitted and watch carefully so you know how to do it next time... hanging a door is fairly straight forward and just needs a systematic approach and some fairly precise measuring and a mastery of a few basic skills and a good "eye" - at least it is all you need when everything is straight... very little in houses, woodwork and life is perfectly square or straight or plumb and overcoming those problems successfully needs a wealth of experience, a good teacher or a sherlock holmes sort of "power of thought"
-
My Roof is Leaking - Roofbond or Traditional Re-roof?
verne replied to johncrowther's topic in Roofing
i am sure we would welcome more information about your roof before you used the foam; was it purely for insulation or did you hope to overcome other problems at the same time, did you spray direct under tiles or slates or is your roof felted? also, how much foam did you use, how much did it cost and how did you apply it? -
i am no expert but 10.5 degrees sounds more suitable for sheet roofing material than tiles... i don't have any input for you about the correctness of your plans. i just wanted to remind you to use only treated timber and it would probably be good to give the plywood a coat or two also. low pitched roofs are often associated with lean-to type buildings. if this is so your water through the tiles might actually be finding ways past any flashing. it is also possible that moss has a good foothold and is beginning to lift the tiles a bit or is separating them... i feel the underlay should either be bonded to the ply in order to completely exclude water or should have a good gap for air circulation between the layers. i have no experience with breathable stuff - but my gore-tex jacket was a huge disappointment. it would cope with generated moisture while at rest or strolling but any effort would have me drenched and took hours to dry (it is a quality police issue jacket) so i am very suspicious about things claiming to be breathable... treating the tiles with a water repellant would probably help them to shed rain more quickly and efficiently thus reducing the chances of leaks and seepage and also reduce frost damage.
-
years ago i bought a huge bag of dry fire clay from our local builder's merchant to line an industrial heater. don't remember how much it was but i do remember it was remarkably cheap. i believe pottery and other types of furnace and kilns are lined with firebrick. maybe someone in stoke could help. there is a famous wood burning bread oven somewhere in the lakes producing specialist breads and distributing nationwide...
Want your website link here? Contact me for pricing