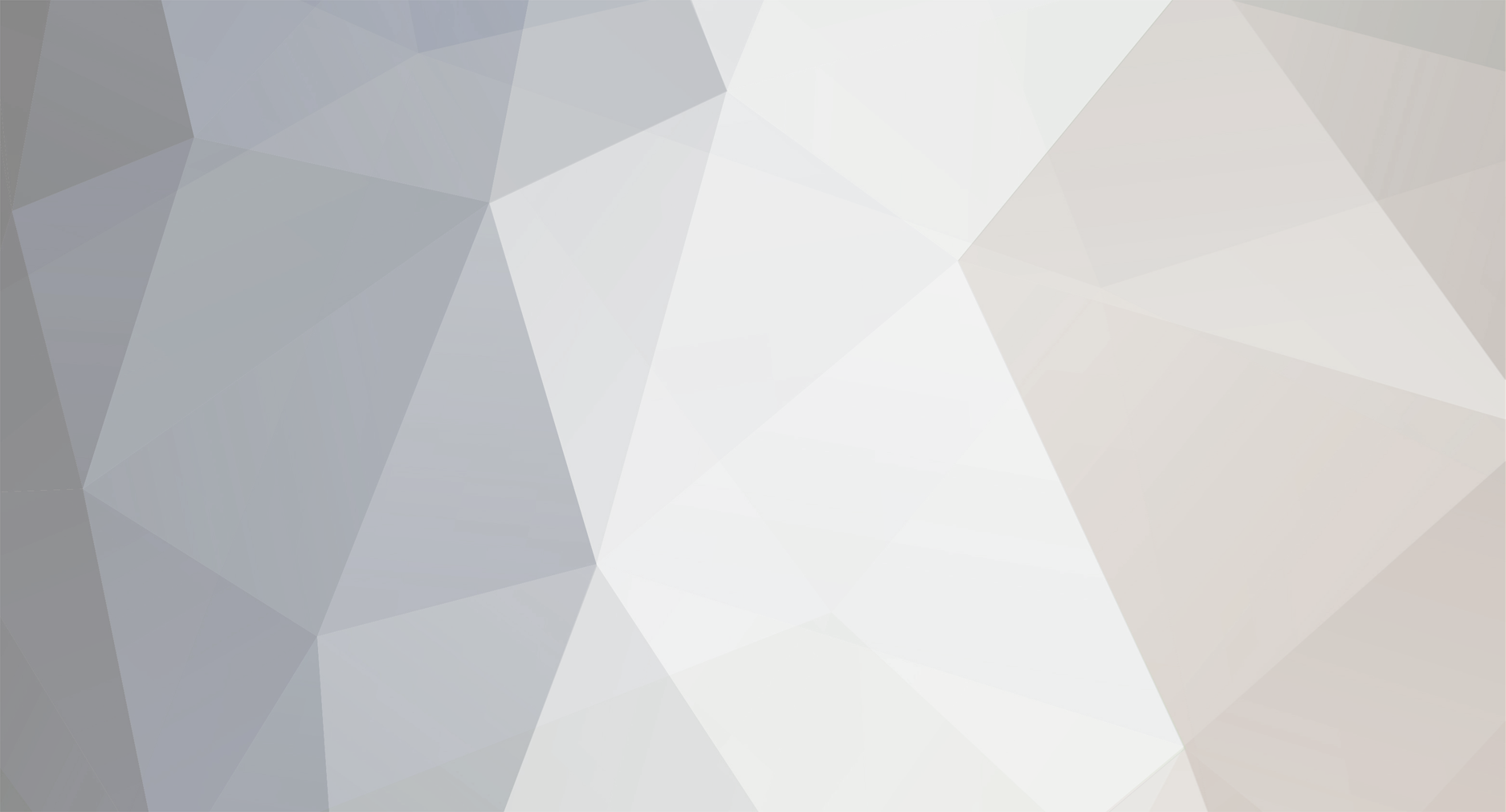
verne
Members-
Posts
74 -
Joined
-
Last visited
-
Days Won
2
Content Type
Profiles
Forums
Gallery
Everything posted by verne
-
mould will always grow where there is food and moisture for it. a lot of it is bad for the health too. i think part of your problem is likely to be your painted walls. modern plastic emulsion paints aren't breathable - in fact they are so good they can be used as an isolator coat between paints of different (incompatible) types to prevent reactions between them... using these for decoration instead of the more traditional whitewashes or limewashes (or nothing at all) will seal off the wall as if you have put a membrane over it, concentrating the escaping moisture into areas where the paint film has an insufficient bond or has otherwise broken down... i suggest you treat your mould with a dilute bleach solution and a scrubbing brush or a proprietory mould remover and forget about decorating until the damp is under control. anti-mould paints tend to be intended for use in areas of high levels of condensation, rather than areas that have a head of water pressure trying to push the paint from the walls. if the injection damp courses have worked well in the other houses, the chances of success with one in your house will be almost assured if it is of the same basic construction, certainly it will help and need not be tremendously expensive. the equipment can be hired to allow a diy job. if enough research is done first on methods, techniques and materials you will at least know that it wasn't a cowboy job... even when you have carried out all the damp reducing measures you can, it will take a long time for the moisture levels to stabilise and the real benefits of it can be seen - possibly a couple of years, or even longer! the vertical damp course is really worth a close look too. if the water table is naturally quite high in your area, rather than the ground being sodden just by drainage problems, you will definitely have to tackle the inside as well as having a close look at the footings if your house has any? a lot of houses do not have proper footings but were built simply on top of the ground, mostly on stone slabs that were set into the ground less than a foot... because lime and dung mortars were used, seasonal movements of the walls did not matter very much. a builder friend has just finished providing his own such house with a nice deep footing. he said it was "steady work" but not much of a problem.
-
i don't know much about stone built dwellings. a lot of the traditional peasant type houses were built of little more than rubble and were always damp and slightly better housing was built with cavity walls that had a decent stone facing but an infill of rubble and rubbish to keep the cost down... i suggest you investigate the possibility of a damp course of some sort before you begin spending much money on the place. an injection damp course probaly wouldn't be very successful alone - depending on the type of stone and construction the chemical would probably only saturate the mortar - but this type would be the cheapest option and would be bound to help. the electro-static damp course has fallen out of fashion and no one can tell me how they work but for most people most of the time they do work, or did work for those who had them. they are almost unknown now but rentokill installed thousands of them back in the 1960's. a deep vee of 3 or 4 inches is cut into the inside walls just above ground level and a continous copper strip is installed, the vee being filled with mortar to secure the strip. the two ends are passed through the wall and joined to a bronze fitting that i don't know the purpose of... fitting a membrane would be a huge amount of work, especially if the walls are thick and do have a rubble filled cavity. if it is possible to carry out some land drainage to reduce the amount of water in the ground around the house, this would probably make a great deal of difference in time, especially with the installation of a vertical damp proof course which will reduce the amount of wall accessible to the wet ground and further reduce the amount of damp. again the vertical dpc is little used now, but can be installed (relatively) quite easily in most instances by digging a short trench against the outside wall to expose the wall down to its footings. the wall is cleaned and rendered with a waterproof render and then covered with what was traditionally slate, but a waterproof membrane would probably be better and could possibly almost make the render redundant. working like this a short section at a time until the entire outside has been circumnavigated. the backfill of each section must be well compacted to ensure the walls remain stable. the same treatment can be given to the inside walls if damp remains a problem and the floors fitted with a membrane and insulation at the same time so your choice of floor coverings is not limited to breathable stuff. alternatively digging out and providing a (ventilated) cavity over which a loose laid concrete block floor is laid will also achieve the same object. please keep us posted.
-
it would be a good idea to try and minimise the damp if you can by attempting to trace the source and then taking a few precautions... an area that is naturally damp must be well ventilated and the source of the damp must not be covered with anything that can't breath... drylining the walls will probably drive more damp into the narrow strip between the floors dampening the woodwork... damp in solid walls can be caused by rising damp bridging the damp course (if it has one) in some way - perhaps by the internal plastering or because the ground level outside is too high or because a porous floor has been covered with something that is forcing an excess of moisture out to the walls. perhaps external rendering is too close to ground level. perhaps the ground is so saturated with water due to a faulty soakaway system or poor drainage. concrete paths too close to the house can cause excessive rain splash where rain bounces up from the hard surface a considerable distance and can saturate a wall above the damp course. damp in solid walls can also be caused by water ingress into the wall higher up and it not being able to escape into the ground because it has a damp course - gutters and downspouts, faulty or porous render can be the culprits. solid walls of old houses do often have damp in them naturally which would normally be kept to minimal levels by evaporation from the exposed brickwork outside. render is only suitable some of the time... if there is a high level of damp in your house you should be aware it does increase the risk of woodworm and dry rot attack. sensible timber treatment and good ventilation is the key to minimising the risk. the importance of open chimneys cannot be over-emphasised...
-
i have never seen one though i wouldn't be surprised if one existed. there are many light level switches available fitted to various devices from street lamps to night lights, including one that plugs in to a bulb holder. i suggest you approach one of the larger electrical wholesalers in your area - they often have access to consultants or at least tend to know their catalogues pretty well... if you get no success there i suggest you contact somebody like farnell or maplin or rs components who i am fairly sure will be able to supply something that could be installed within a switch.
-
the simple answer is - you can't! as far as i know there are no products that bond tiles to fresh air. i suggest you carry on removing the grout and any tiles not securely fixed until you have discovered the extent of the problem - then attempt to remove a few more tiles so you have an area of good solid plasterboard around the hole that it will be necessary to make by removing the sodden plasterboard. give it some drying time so your repair is not going to trap any moisture where it can cause long term damage. clean the edges of the resulting hole. don't worry if the hole isn't a regular shape - plasterboard repairs are more successful with irregular shapes as it provides more bonding area around the edge... if it is a stud wall with a cavity behind it you will need to provide a shoulder to prevent the patch from falling through the hole. you can do this by bonding some bits of board to the back of the existing plasterboard at convenient intervals around the hole leaving an inch or so protruding into the hole area... if it is a battened wall you can use the same method or provide extra battens or use a combination of the two methods. cut a patch to fit the hole from some board of the same thickness, but slightly smaller to leave a 3 or 4mm gap all around for the no-nails adhesive. glue (pva or similar) the patch into place against the shoulder and using spacers around the edge to maintain the gap until the glue is holding and then insert a bead of no-nails around the edge... if your plasterboard is just a dot and dab cladding over a solid wall it will be straightforward to provide a few dabs of adhesive and settle the patch until it provides a flush surface. the hard bit of the job will be removing the old tile adhesive without breaking any...
-
the victorians, like many from before and after, built many very good houses - but also threw up a lot of rubbish! a lot of the rubbish from the barratt type builders of those days is still standing - and i am living in one of them now. perhaps you are too? building materials were fairly expensive in those days, so was labour - in fact things weren't much different from now except there was no diesel lorries to haul stuff around and there was no power tools to make work quicker and easier. houses that were built for the letting market would have as many corners cut as were needed to bring them in within the budget... substandard mortar, bricks re-used from previous demolitions, substandard bricks, inner walls would be where any brick ends, cobbles and odd lumps of coal would be used up. the further up the house and at the back of the house was where most of the cost saving took place. a lot of money was saved by using second and third grade timber and adze cutting the rough sawn boards to fit - a lot of money was saved by having floorboards only planed one side... a lot of such houses were built without proper foundations or incorporating bits and pieces of the foundations of previous houses... half a ton would be a lot of weight to put on a floor upstairs if your house was without any defects. it would probably stand it quite safely until the floor began to become permanently warped as timber will if it is subjected to a great load for a long time. my concerns are about the unknown factors of the timber grades and the quality of the building and of the foundations. my advice is don't! if you must go ahead then pay a professional to look at it first so you can sue someone if there is a problem... if you have sufficient ceiling height in the room below you could strengthen the floor and spread the load into all the walls by installing more joists at right angles to the originals and underpinning your floor. you can then enjoy an open beam look or intall a new ceiling... alternatively a couple of nicely painted acro-props would provide extra support.
-
quickest and easiest thing to try first would be to use a different type of fire caulk. there must be many different types on the market with varying degrees of flexibility for different purposes. the problem is probably caused by the existing caulk being too rigid. i suggest you do some research into the local building and fire regulations where you are and find the purpose of that caulking; is it merely to stop smoke or is it to give a 30 minute fire barrier - or longer? armed with the correct requirements you can then approach some suppliers with your problem and requirements and obtain some really professional suggestions. one interesting solution which could allow a clearance for expansion is to use an intumescent sealer which would expand and seal the gap in the event of a fire... i believe there is also a variety of flexible and semi-flexible collars available for many types of pipe... even some of the high grade silicone sealers are resistant to some very high temperatures but remain very flexible - even in permanent contact with car exhaust systems... it probably was not necessary to use that method of sealing in the first place to overcome the problem. it was probably done that way to cut building costs. prepare for some resistance from the guys who have to fix it.
-
hello. traditional deep shine finishes take a lot of time and skill to achieve, although french polish takes considerably more skill than using coloured varnishes or stained wood and clear varnishes. i have produced some "nearly" french polish finishes with varnish by applying six or eight coats and flatting between coats using a fine wet or dry paper and a rubber block. the first couple of flattings were carried out dry with a 400 grade and thereafter wet with 600 grade. the last but one coat was flatted with 1200 grade with soap and water. the last coat had to be done in a very clean place with very clean materials and tools to eliminate the need to de-nib the final finish and the resultant polishing, although fine abrasive compound polishing will enhance the shine. modern mass produced stuff has more in common with car spraying than with traditional brush finishes. a cureable laquer is sprayed in huge volumes which buries minor surface defects and finds its own level while still semi-liquid but curing quickly in the same way araldite or body filler cures. the really hard finishes use some nasty chemicals in the curing process which means air fed breathing apparatus must be used, rather than just a face mask. i suggest you have a word or two with a painter at a local spray shop for suggestions. he will probably direct you to his paint supplier who should be able to mix a synthetic laquer to match your existing colour...
-
Replastering ceiling and spotlights...
verne replied to mgwdiynovice's topic in Plastering and Boarding
as long as you know exactly where your lights are going to be sited i think plaster first... if you are going to have to dig around a bit to avoid joists, it would be a good idea to to that before the plastering. might be a good idea to ask the plasterer what he thinks - plasterers aren't normal people and they tend to bite when upset... -
thanks for that info. i've not seen any clear stuff yet - pink and brown, and the stuff i generally use is the (almost the cheapest) white water based which does the job around the house ok. the stuff you speak of might be useful at work. sometimes things need to be stuck that would normally need a polyuerethane structural type adhesive which is expensive and has a very short life once the tube is started. i will buy a tube of clear and give it a try...
-
just a reminder to make certain the light/power is switched off first. when a bulb has failed it is easy to forget this little detail or become confused if there is more than one switch... water based no-nails will probably take longer than 15 minutes to set sufficiently due to the lack of absorbency of the materials to be stuck together. due to the difficulty of sticking glass to anything because of its smoothness its probably a good idea to scuff the surface a bit with some scotchbrite or fine wet-or-dry paper before you begin.
-
750mm is a wide span for a single louvred door. the construction of that type of door is not strong and to remove more than an absolute minimum of material for fitting is to invite problems for the future... i suspect the only way to fill the door hole with just one door would be to have one made especially for the purpose. who ever made it for you would probably have a good holiday this year on the proceeds... even using the double doors you have found would mean removing more than just a shaving or two from each door. in order to make them fit and have a couple of mm gap all around will mean removing 4 or 5 mm from the verticals and at least 40mm from the horizontals and could be more if your floor is carpeted... if the doors you have found are of particularly good quality you might get away with it, but i suggest you check with the supplier first. tell him your intentions and ask him if it will affect the warranty regarding warping and twisting... a more substantial solution would be to use a smaller size of louvred panel or panels, depending what is available and either have them fitted in place of the panels in a stock sized four or six panelled door or to have a substantial frame put around two smaller panels of a size to fill the space. it would still cost quite a bit though... it is not easy to give detailed instructions on door fitting in a post like this. there are quite a lot of how-to videos available. some are free off the internet. if you haven't a clue, then you probably don't have many tools either. might be a good idea to pay to have this one fitted and watch carefully so you know how to do it next time... hanging a door is fairly straight forward and just needs a systematic approach and some fairly precise measuring and a mastery of a few basic skills and a good "eye" - at least it is all you need when everything is straight... very little in houses, woodwork and life is perfectly square or straight or plumb and overcoming those problems successfully needs a wealth of experience, a good teacher or a sherlock holmes sort of "power of thought"
-
My Roof is Leaking - Roofbond or Traditional Re-roof?
verne replied to johncrowther's topic in Roofing
i am sure we would welcome more information about your roof before you used the foam; was it purely for insulation or did you hope to overcome other problems at the same time, did you spray direct under tiles or slates or is your roof felted? also, how much foam did you use, how much did it cost and how did you apply it? -
i am no expert but 10.5 degrees sounds more suitable for sheet roofing material than tiles... i don't have any input for you about the correctness of your plans. i just wanted to remind you to use only treated timber and it would probably be good to give the plywood a coat or two also. low pitched roofs are often associated with lean-to type buildings. if this is so your water through the tiles might actually be finding ways past any flashing. it is also possible that moss has a good foothold and is beginning to lift the tiles a bit or is separating them... i feel the underlay should either be bonded to the ply in order to completely exclude water or should have a good gap for air circulation between the layers. i have no experience with breathable stuff - but my gore-tex jacket was a huge disappointment. it would cope with generated moisture while at rest or strolling but any effort would have me drenched and took hours to dry (it is a quality police issue jacket) so i am very suspicious about things claiming to be breathable... treating the tiles with a water repellant would probably help them to shed rain more quickly and efficiently thus reducing the chances of leaks and seepage and also reduce frost damage.
-
years ago i bought a huge bag of dry fire clay from our local builder's merchant to line an industrial heater. don't remember how much it was but i do remember it was remarkably cheap. i believe pottery and other types of furnace and kilns are lined with firebrick. maybe someone in stoke could help. there is a famous wood burning bread oven somewhere in the lakes producing specialist breads and distributing nationwide...
-
my plumber mate speaks a lot about repairing boilers. he says choose a boiler expecting it to go wrong sometime - how easy is it to service and repair? how much are the spares and how easy are they to buy locally? most new boilers of the correct specification will be ok for a year or two but i have heard all sorts of horror stories about dodgy heat exchangers that rot soon after the warranty expires and cost more than a new boiler to replace and a complicated boiler having complicated problems and the owner being without heat or hot water while waiting for a specialist to arrive from the other end of the country... diy guy is right - talk to a few plumbers and always remember "to get the right answer you must first ask the right question". popular boilers often do not represent the best buy, but often merely represent the model that makes most profit for the supplier... i opted for an ideal standard boiler on the grounds that i could afford to mend it because the cost of circuit boards and such like were very expensive for many of the fashionable high tech brands of boiler.
-
i would suggest you have a close look at it. after 5 hours it should have been fairly firm and if it didn't rain hard it shouldn't have done much damage. if the rain did penetrate the screed i think the damage will be obvious - if it looks ok, then it probably is ok.
-
survey won't let me in without a user name and password!!! biggest problem with cordless tools for diy is they don't get enough use to give the batteries a good enough run for your money. batteries left discharged for long periods are soon ruined and who can control where they are dumped? diy cordless tools are cheap enough to replace which is good, but does not encourage people to look after their tools... more tradesmen just chuck their old stuff into a skip than recycle properly... it is the current fashion for corded tools to be as big and heavy as possible which makes them really unsuitable for most diy tasks - hence the popularity of cordless tools. if it was possible to buy a small and light corded drill similar to the old wolf cub i would prefer to use that sort of tool most of the time - as would most of the trades people (in their workshops) i have spoken to about this matter. i only buy 12 volt tools so that when the battery fails i can use them from a car battery or just wire them to a decent battery charger. the artificially inflated cost of replacement batteries amounts to a restrictive practice by the manufacturers and creates a great deal of unnecessary waste... silverline tools have a 3 year guarantee and some of their cordless drills have battery packs that are detachable so they can be worn on the belt and are fed by a curly wire lead. the nearest thing i have seen to a corded cordless tool. the replacement batteries and chargers are also reasonably priced - so says a tradesman friend of mine who bought one for use up the ladder in case he dropped his makita...
-
clearly the items illustrated are high quality components but for £150 they should also be gold plated and studded with diamonds... i have seen something like this before but cannot remember where and it is bugging me. got a feeling it was something to do with some equipment made for the disabled... there is a company called pera in melton mowbray who specialise in developing products for other companies. it is possible they have a database of useful bits and pieces. another company called rs components supply a huge amount of unlikely stuff as well as the electronic gear they are reknowned for... alternatively a walk around your local industrial estate asking daft questions might prove fruitful. if your project does not require such high quality; it would probably be cheaper and easier to have them manufactured locally. there is still engineers who will produce short runs of items on manual machines. depending on the strength and accuracy required they could either be part machined/part fabricated from sheet and use stock fasteners or wholly machined from a variety of materials from stainless to solid teflon. holscot, here in grantham, is the king of teflon.
-
thermilate insulating paint additive anyone?
verne replied to james007's topic in Painting & Decorating
about 35 years ago my father bought some rolls of thin expanded polystyrene to use as a lining paper at my gran's house. i don't know how much less coal and wood they burned on their black-leaded range but it did remove the severe cold shock if one accidentally touched a wall... still available?? -
pictures are not incredibly clear of the second switch. there does seem to be a problem with the wiring of the second switch. two way switching is relatively straightforward - the switches are connected by a three core cable with the common terminal of one switch being the live into the system and the common of the other switch going to the light. the other two switch terminals are connected individually, usually by the blue and yellow wires, to the opposite numbers of the other switch. the picture of the second switch shows a red wire sharing the terminal with the yellow wire. i think this is probably the fault. there is no reason for this... perhaps someone was trying to pick up a switched live to feed the second light or something. unless you can say whether that wire is live or not and whether that switch common is on the live end of the circuit or the lamp end i wouldn't be happy about commenting further. what you really need to do is identify the function of as many of the wires as you can until you have a clear picture of the circuit in your head. the reason for the extra wire should then become clear, along with the place the person really intended it to go...
-
suggest you determine whether your lights are wired in the modern fashion; the supply leapfrogging from ceiling rose to ceiling rose - the extra terminals in the modern rose being used to replace junction boxes, or whether junction boxes are used exclusively, or a combination of both. you might have to unscrew and pull down some ceiling roses to check. when you have an idea of where the supply enters the dead lighting circuits, and the route it takes, it should be fairly straightforward to determine if the fault is within that circuit or with the supply from another lighting circuit; progressively closer to the consumer unit. single strand cable sometimes breaks or works loose where the terminal screw is tightened against it, due to poorly machined screws, overtightening and the repeated heating and cooling or other movement or vibration and the natural tendency for copper to age-harden and work-harden and become brittle... chasing an interruption in the supply can be a bit tedious. if junction boxes are used it will probably be necessary to lift a few floorboards. mostly such problems are straightforward and usually found at or near to a terminal. best of luck.
-
Roof Problem - Damp, Bats, Broken Mortar - See Photos...
verne replied to johncrowther's topic in Roofing
firstly, the white pot hanging thing is an aerial insulator. i have several. old radios needed a good dipole aerial for decent reception over a large part of the country and you have found a remnant of one of those. i reckon you have about hit the nail on the head with your theory about condensation. most houses have some big air currents - do cooking smells roam around the house? if they do you can guarantee everything else does too. gas ovens produce huge quantities of water vapour and people produce gallons. if you have a limited number of open chimneys/fireplaces and not much alternative ventilation you are asking for troubles (black mould, chest infections,etc). indoor drying is likely to be only aggravating an existing problem. the straw like stuff looks like the reeds that used to bed my tiles before we had it stripped. our top floor ceilings also used reed and plaster instead of lath and plaster. the floors of our top storey is also reed and plaster. i am wondering why you have these in your attic - maybe the slated roof is not original? such a tiled roof has a lot of mortar. as the reed bundles fail and the tiles begin to sag dabs of mortar and oddments of brick, etc. are used to prop them up and fillets of mortar are used to stabilise damaged tiles to prevent them sliding. difficult to see from the photo but the amount of scrap slate and the way it is gathered in one or two confined areas leads me to believe they are roofer's trimmings rather than what has dropped through deterioration of the slates... further evidence your roof is not original comes from the picture showing a definite line or change between your roof and your neighbour's. your roof appears to be fairly dry but as it is not felted there will be times when some water will find its way in. the combination of moss and frost will damage the slates and make them porous. wind and other vibration will eventually loosen an odd slate and allow it to slide... the white stuff looks like efforvesence which is evidence of some water ingress at some time. first time it rains hard i suggest you make another pilgrimage upstairs. the white spores might be nothing or might be dormant dry rot waiting for moisture to allow them to get going. dry rot is fascinating stuff and a ripe fruit is quite attractive. it is probably nothing but we must be vigilant about such things, especially as the weather becomes milder and damper. -
My Roof is Leaking - Roofbond or Traditional Re-roof?
verne replied to johncrowther's topic in Roofing
if your roof is felted under the tiles the polyeurethane foam or whatever they spray on cannot hope to bond the tiles together unless they cut or tear away the felt first... this could then be a good way of stabilising a failing roof - as far as the bits between the rafters is concerned! any leaks above the timbers is unlikely to be sealed leaving the timber open to attack by nasties. a few soffit vents are unlikely to help. i think this process is best suited to insulating steel based industrial type roofs and kept away from timber and tiles (probably how they have remained in business 40 years). it might be ok making a good roof stay good for longer but i think it should be kept away from a failing roof. a dislodged tile or one holed by frost is unlikely to cause a troublesome leak if the underfelt is ok - so it probably isn't that good. some roofs weren't felted at all when new. quite alarming to be able to bird-watch through the gaps but watertight except in driving rain, and snow was a bit of a problem. our tiles were laid on bundles of reeds which would have lasted more than the 130 odd years if jerry hadn't chucked a few bombs at our street... if good secondhand tiles are available to match your own you have an extra option available to you - having the roof stripped, refelted and relaid, which can be a big saving over the cost of a re-roof. it could be as little as half the cost. get together with a neighbour so the scaffold doesn't have to be moved far and the cost continues to fall, especially if you choose a roofer with his own scaffolding. i suggest you take a flask of coffe up into your roof space and examine the underside of your roof to see what you can learn; as well as deciding for or against timber treatment against worm and measuring for additional loft insulation. could be you might be eligible for some grants... some research about the reputation of local roofers would be in order... try finding out which one has the contract to maintain the local public buildings or ask your local builders merchant to suggest a couple... -
thanks for that. i will look out for some. it sounds like the sort of stuff to make the wife a new winter coat from and help save the planet... the staples would probably hurt though!
Want your website link here? Contact me for pricing